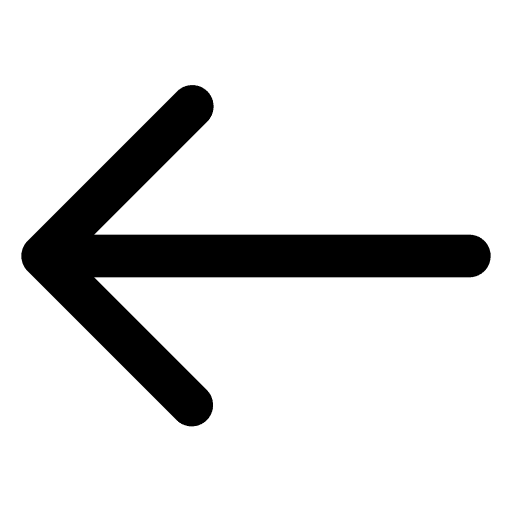
Helpful Tips: Heat Sealer Troubleshooting
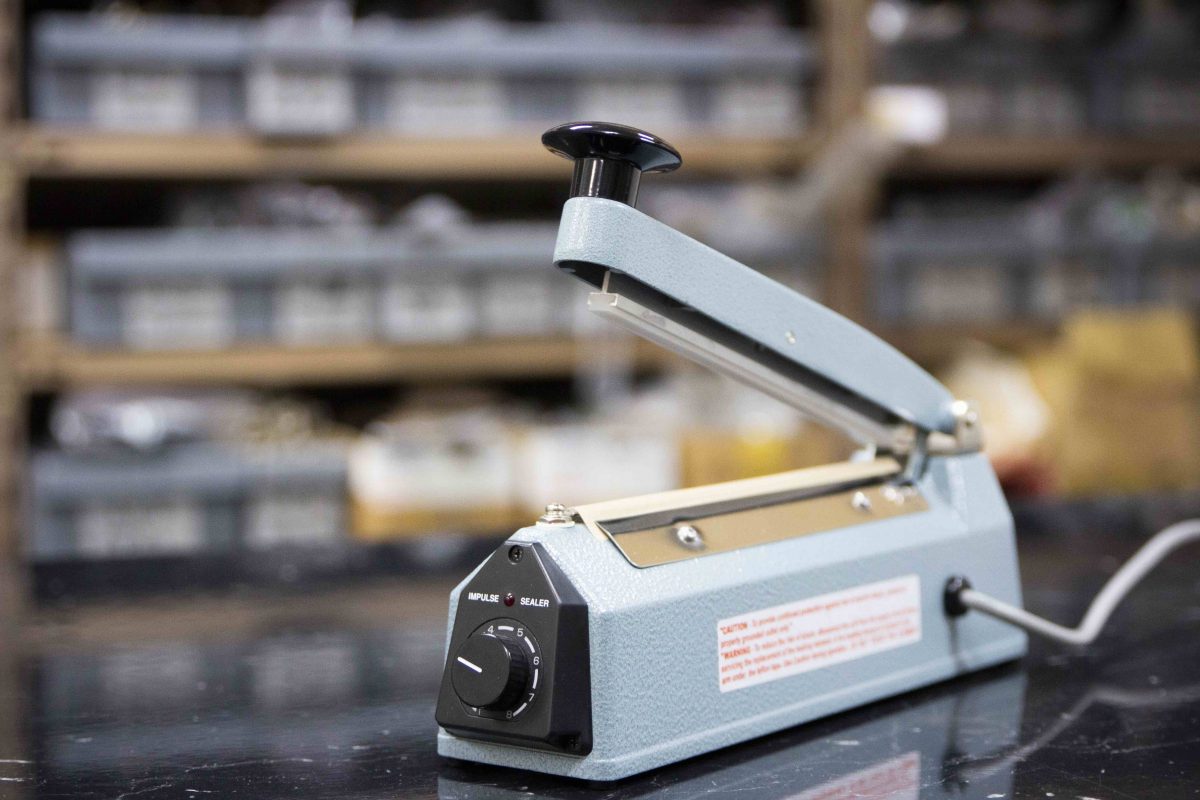
Troubleshooting guide for your Impulse Heat Sealer :
1. What type of heat sealer do you have?
There are two types of heat sealers; the first, and most common, the Impulse Heat Sealer, which seals bags using an ‘impulse’ of electric voltage that heats a nichrome element and the PTFE strip that seals your product; the other, a ‘constant’ heat sealer, where the heating/sealing jaws are constantly hot. We are discussing the Impulse Heat Sealer in this article.
2. What types of bags/tubing are you using?
Impulse Heat Sealers will seal all LDPE, PP, and some laminated bags/pouches, but they will NOT work with cellophane bags, a steady state constant heat sealer is required to seal this type of material.
3. How long is your heat sealer?
It is important that the Heat Sealer you are using is the right length for the plastic bag that you are sealing. That is, don’t use a 400mm heat sealer to seal a 100mm bag. Impulse heat sealers heat up upon pressing the arm down and the generated heat from the action is used to heat and seal the bag. If a large area of heat is left unused, this will keep accumulating in the Teflon without dissipating. Eventually, the PTFE and element will burn out very quickly as the heat is not being released.
4. If you are using a bag which is a good deal narrower than the width of the sealer…
then the unused Teflon and element wire could be covered with a scrap of polyethene or aluminium foil to soak up the heat to stop the element wire, PTFE, and silicon from overheating and burning out.
5. How are you using the timer?
Test for the best timer setting before commencing work. For thicker bags/tubing, you will need to set the timer to a higher setting.
6. Do you use excessive force on the top bar when sealing poly films?
It is the heat sealing the bag, not the pressure you place on the arm of the heat sealer.
7. Do you wait for the buzz?
Make sure that when you press on the arm that you wait until you hear the ‘buzz’ before lifting the arm back up. Not waiting leads to an ineffective seal, build-up of residue and damage to the heat sealer.
8. Have you checked the condition of your heat sealer parts?
Regularly check the condition of the upper and lower PTFE tapes. Remove the upper Teflon tape and inspect the element and lower PTFE Tape. If any of the PTFE tape has signs of burn, wear, or damage, then replace.
Watch the video on changing PTFE tape and element wire.
Regularly check the condition of the silicon rubber in the upper jaw, if there are any signs of burn, wear, or visible damage, then replace the silicon rubber.
9. Did you hear the click of the micro switch?
Listen to the click of the micro switch when attempting to make a seal. If there is no click audible, then the micro switch could be out of adjustment or in need of repair.
10. Did the light timer come on?
The micro switch activates the light on the timer. If the light does not come on while attempting to heat and seal, then the timer unit may be in need of replacement. This is assuming that there is electricity at the outlet and the machine is plugged into a wall socket and the power cable is in good condition.
11. Are all surfaces clear of residue?
Always ensure that the sealer surfaces are clear and free of any residue and contamination.
All spare parts are available from our Service Team and can be sent to you via overnight delivery if required. Please call our Service Team on (03) 9428 1652
For further details or to speak with a sales consultant:
Call (03) 9428 1652 or email us at venus@venuspacking.previewsite.com.au. For more information on our products, visit www.venuspack.com.au